
.jpg)

TELESCOPIC PORTABLE RADIAL CONVEYOR
AS THE ORIGINAL INVENTOR OF THE TELESCOPIC STACKER, THOR GLOBAL HAS EXCEEDED EVERY REQUIREMENT BY DEVELOPING NEW AND INNOVATIVE DESIGN FEATURES FOR INCREASED PERFORMANCE, DURABILITY AND SAFETY. STANDARD FEATURES MAKE THE THORSTACKER™ THE MOST ALL-INCLUSIVE, HIGH-END TELESCOPIC CONVEYOR ON THE MARKET.
FULLY BRACED
Patented Fully Braced Undercarriage allows the upper and lower portion of the undercarriage to be fully braced at all times, even when completely raised. Available on select models.
STRONGER SUPPORT
Patented LES (Load Equalizing System) provides a structure with greater support and longevity under the stresses of heavier loads.
FLEXIBLE, EFFICIENT
Fully automated functions provide increased flexibility, accuracy, and efficiency.
USED IN THESE INDUSTRIES: AGGREGATE, AGRICULTURE & RECYCLING

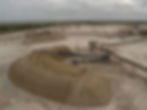
T110x36-0800
T130x36-0800/1000
T150x36-0800/1000
T170x36-0800/1000
T190x36-0800/1000
T130x42-1200/1500
T150x42-1200/1500
T170x42-1200/1500
T190x42-1200/1500
T130x48-2000
T150x48-2000
T170x48-1500/2000
T190x48-2000
T150x54-2000
T170x54-2000
900 mm
900 mm
900 mm
900 mm
900 mm
1050 mm
1050 mm
1050 mm
1050 mm
1200 mm
1200 mm
1200 mm
1200 mm
1400 mm
1400 mm
CAPACITY
800 stph
800/1000 stph
800/1000 stph
800/1000 stph800 stph
1200/1500 stph
1200/1500 stph
1200/1500 stph
1200/1500 stph
1200 stph
2000 stph
2000/2200 stph
2000 stph
2000/2200 stph
2000 stph
LENGTH
115 ft
140 ft
150 ft
170 ft
190 ft
135 ft
140 ft
150 ft
170 ft
190 ft
135 ft
140 ft
150 ft
170 ft
170 ft
BELT WIDTH
MODEL
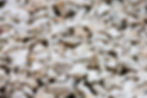
STANDARD FEATURES
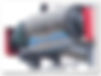%20%26%20Tensioning%20system.jpg)
Belt Scrapers (Twin-Edge) & Tensioning System: Patented
Situated at the discharge end on both conveyors, Thor’s exclusive twin-edge belt scrapers are designed for a cleaner return and longer belt life. All scrapers are manufactured using a tough ¾” thick, 10” wide urethane blade combined with an extension spring. The blade is reversible for double lifespan. The PATENTED belt scraper tensioning system provides maximum control and better usage of the blade.

Belt Splice: Vulcanized
All belt splices are vulcanized in house to ensure greater belt life for all of our end users. Vulcanizing also prolongs the life of the belt scraper. Thor Global uses premium quality and high tensile strength belting.
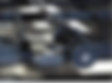
Cable Slack & Tension Detection
The cable slack and tension detection system utilizes the PLC to constantly monitor cable tension and alert the operator when the cable needs to be adjusted. This failsafe system is easily accessible when adjustments are required. All machines use standard 9/16” cables to add strength and reliability.

Contactors: IEC
Thor Global is very aware that bulk material handling environments can be extremely harsh on electrical components. This is why the conveyor uses over sized IEC contactors for all applications to provide a more robust system

Electrical Cable Harness Pulley: UHMW
Custom made UHMW pulleys, which are attached to the electrical cable harness that supplies the inner truss, are guaranteed not to seize up.

Emergency Braking System
In the unlikely event of winch cable breakage, the braking system is immediately engaged, preventing the inner truss assembly from traveling backwards. The emergency braking system will prevent excessive damage from occurring and more importantly eliminates the risk of injury to any individual.

Gear Reducers: CLASS 2
Dodge, always CLASS 2 with no need to upgrade from CLASS 1.

Hydraulic Cylinders: Single Stage
Single-Stage hydraulic cylinders provide a simple, more reliable solution than complex multi-stage hydraulic cylinders.

Head Undercarriage (all braced): Patented
The patented all braced Undercarriage allows the upper and lower portion of the head undercarriage to be fully braced at all times, even when completely raised. The hydraulic lifting cylinders have a wider stance and are in-line with the HSS (Hollow Structure Steel) tubing to provide greater stability. Restriction stoppers have been applied to the all braced Undercarriage to maximize the efficiency of the hydraulic cylinders and protect the hydraulic system from overloading. Additional cross bracing on the upper head undercarriage as well as added protection around the hydraulic lifting cylinders both contribute to a machine that is superior in strength and longevity. This is potentially the strongest head undercarriage ever built! Standard on select models. *Select models include T150x42-1200/1500, T135x42-1200/1500, T170x42-0500/0800/1000 and T150x48-2000.

Idlers: CEMA C
Strongco CEMA C idlers are standard on all machines. They are intended to last twice as long as CEMA B. Thor uses nothing less than the best!
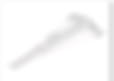
In-line Swing Axle
The exclusive inline swing axle design is the only system that enables the machine to radial in a smooth motion without straining or scuffing the tires. The wheels remain in a perfect arc because they are in-line or side-by-side at all times. The axle design is 27ft in radial mode providing the most stable structure on the market.

Inductive Proximity Sensors
Inductive proximity sensors utilize the PLC to accurately track the radial drive and telescopic position of the conveyor, providing increased flexibility in determining radial travel and extension/retraction parameters. The radial drive sensor is located on the non-drive side of the wheel to guarantee accuracy.

INOVUS Automation Technology
INOVUS Automation Technology uses various sensors connected to a PLC in order to perform the following automated functions: Pile Detection & Material Flow (Standard) Radial Drive & Telescopic Position (Standard) Cable Slack & Tension Detection (Standard) Belt Tracking (Optional) The most unique function of Thor’s INOVUS Automation Technology is the ability to change parameters “on-the-fly” during automatic mode of any program.
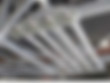
LES: Patented
The patented LES (Load Equalizing System) was engineered to evenly distribute the constantly changing load of the inner truss as it extends and retracts. When extending and retracting a telescopic, the forces applied to the inner structure can be very high. The system uses a unique 4-roller design to effectively distribute this load over the entire inner structure. The LES is located under the inner conveyor to avoid material build up. The combination of the upper and lower LES keeps loads even on all 4 rollers for worry-free operation.

Limit Switches: NEMA 4
NEMA 4 rated back-up safety switches are located in various positions across the stacker. Weatherproof seals ensure that the switches operate reliably under harsh conditions, thereby eliminating potential downtime.

PLC: MICROLOGIX 1400
The automation control system uses the legendary bulletproof Allen-Bradley MicroLogix 1400 Control System with an ethernet port for web server compatibility and a built in LCD for I/O status control. The system is powerful, reliable and flexible.

Program: Windrow Auto Mode
Thor Global’s basic programming was originally designed to minimize segregation by stockpiling material in concentric rows called windrows. The operator has the ability to set specific parameters based on a radial degree limit and extension retraction limit.

Push Button Control
As a preventative measure, Thor Global has applied basic push button technology in addition to the standard touch screen system to provide a failsafe back-up system for increased comfort and reliability.
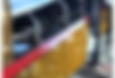
Safety Guarding
Galvanized steel mesh guarding surrounding the main conveyor and safety guards at all pinch points provide ultimate protection for all operators and personnel within close range of the conveyor.

Side Guide Rollers: UHMW
Thor Global’s more forgiving UHMW guidance system does not employ metal on metal contact and covers the entire height of the inner chord prolonging the lifespan of the inner telescopic.

Steel: 60,000 psi
Thor Global uses 60,000 psi yield strength steel versus the industry norm of 45,000 psi yield strength for all HSS (Hollow Structural Section) tubing. This FINER grain steel provides additional strength without additional weight.
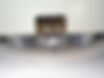
Stone Box Skirting (Floating): UHMW
Located between the stone box and the conveyor belt, the UHMW skirting is designed to “float” on the belt via slotted holes, maintaining a constant point of contact, thereby minimizing spillage and wear due to friction.
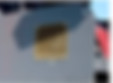
Tail Pulley Access
An opening located on the counter weight allows safe visual inspection and greasing of the tail pulley bearings during operation.

Tail Pulley Kicker Bar
A kicker bar is attached to the tail pillow block bearings of the inner and outer conveyors to keep material off the pulley, which prevents tracking and belt damage.

Tail Undercarriage Hinge Point
This original Thor design removes all lateral stress from the radial arms, as the unit is being raised or lowered. The extended hinge point enables the onveyor to raise and lower “on-the-fly” (without stopping the machine), which effectively helps to provide segregation free material..

Touch Screen Control: HMI08CE
The touch-screen control provides a simple to use and fully automated program for setting parameters and pile configurations. All controls are on the same screen. Cutler-Hammer touch-screens are NEMA 4 rated and very durable, withstanding a shock load of 30Gs. These screens come with standard replaceable overlays, to ensure a clear view.

Touch Screen Sun Visor: Anti Glare
An enclosure around the centric control system removes glare for increased touch-screen visibility.

Training: Onsite
A factory trained, Thor authorized representative will be on site to ensure that you and your operators know all there is to know about how the conveyor operates.

Transport Auxiliary Axle
The axle is a specially designed outrigger style framework with 8 radial tires mounted onto standard 10-stud hub and transportation/truck spindles, bearings. Wheels are equipped with air-actuated brakes for transport. An auxiliary axle is included where required by law for road restrictions.

Transport Flip Box
Kingpin, counterweight and side plate assemblies are designed to allow ample turning clearance for most 5th wheel tractors, as well as easier and quicker hook-up from operating to transport positions.

Transport Mobility
All portable conveyors (including the T190 series) are designed to stay within most transportation regulations. The machine can be folded up and ready for transport in under 12 minutes.

Ultrasonic Sensors
Ultrasonic sensors utilize the PLC to automatically maintain a pre-determined drop distance from the head pulley to the stockpile as well as stopping all radial movement when no material is detected on the conveyor belt. These sensors never come in contact with the material and are maintenance free.
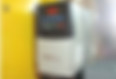
Variable Frequency Drive
Variable frequency drive provides smooth acceleration and deceleration of the, eliminating jerky or jarring starts and stops. The VFD (Variable Frequency Drive) also allows the operator to adjust the radial travel speed.
OPTIONAL FEATURES

Anchor Pad: Portable
Thor has developed a strong steel fabricated anchor pad that is very compact and portable. The anchor pad conveniently fits into the receiving hopper for transport.

Colour: Custom
We understand the importance of corporate image, so we at Thor Global will always try to meet the specific requests of our customers as best as we can.

Dual Drive
An optional second radial drive allows the conveyor to maintain traction in the most demanding conditions.

Chute: Custom
A standard box shaped design has tapered sides with a wider feed opening. Other custom designs are available upon request.
Contactors & Starters: NEMA
NEMA rated starters and contactors are available upon request.

Galvanizing: Hot-Dip
Realizing that some customers have to work in harsh environments with corrosive materials, Thor is the first and only manufacturer to provide a unit that can withstand your tough environment. Machines are fully Hot-Dip galvanized before assembly. Hot-Dip Galvanizing relieves the internal stresses of welded components, providing a fully stress relieved structure. Zinc has a very high relative corrosion resistance.

Program Package: Zero Segregation & Max Pile Auto Mode
Zero segregation programming is recommended when minimizing segregation is of the utmost importance. The primary function of zero segregation programming is a stepping function, which prevents material segregation along the outside of the pile in addition to the inside of the pile. The most unique function of Thor’s zero segregation program, is the ability to control the degree of step, which enables you to control the exact size of the pile. Max Pile programming is recommended when segregation is not of any importance. The conveyor minimizes all movements in this auto mode.
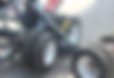
Push Down Axle: Patent-Pending
Hydraulically operated “push down” axles lift the machine to allow quick and easy movement of the machine without the need to move the main axle from radial to transport mode.
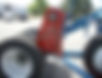
Quick-Release System
This system allows the operator to easily engage or disengage the chain drive system for travel or working positions within less than 3 minutes, minimizing set-up and tear down time. This chain does not need to be taken apart when putting it on or taking it off the wheel drive sprocket.

Tow Hitch
The tow hitch provides quick and easy movement within the worksite.

Transport Landing Legs: Hydraulic
Hydraulic landing legs provide the same benefits as regular landing legs with the added flexibility of lowering the conveyor into operating mode after it is unhooked from the transport truck. Hydraulic landing legs may also be used to raise the conveyor onto a transport truck.

Transport Landing Legs: Regular
Landing legs are required when loaders are not available to lift the conveyor off the truck. These Landing Legs allow you to unhook the conveyor from the transport truck without the need for additional equipment.

Wire Remote Touch Screen: Dual
Dual wire remote control involves keeping the touch screen panel on the conveyor and adding a second panel up to 1000ft away from the conveyor. A selector switch is applied to control which control station is active. Dual wire remote control provides increased versatility.

Wire Remote Touch Screen: Regular
A wire remote control may be installed for applications with a control tower or station. This involves removing the touch screen panel from the conveyor and reinstalling it up to 1000ft away from the conveyor. Wire remote control provides increased visibility of overall operations.

Wireless Remote Control
This system allows wireless remote control operation of the conveyor for movements such as telescoping in and out, or luffing and slewing. Wireless remote control provides increased visibility and flexibility. Wireless remote control is ideal for ship loading applications where visibility from the main control panel is limited.
SPECIALTY FEATURES
Belt Alignment Sensor
A belt alignment sensor may be applied in connection with the PLC to monitor the belt alignment and alert the operator when an adjustment is required to further extend belt longevity. Also known as belt tracking.
Belt Scrapers: H/D
HD (High Definition) belt scrapers are available upon request. Includes 2 primary and 1 secondary blade.

Mobile Track Unit
The mobile track unit is a versatile solution for moving a conveyor quickly and safely on location. The unit acts as a fully functional anchor pad, thus eliminating the need for an external anchor pad. It can be fitted with an external electrical power supply hookup or an independent diesel genset engine. Optional wireless remote operation capabilities are available upon request. All units are wired directly to a push button control box, which is configured with two speed settings (85 fpm and 170 fpm). All units are also equipped with an emergency stop push button. Thor mobile track units can also be used with other types of equipment using a 5th wheel hookup.
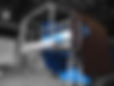
Platform
A platform has been designed to attach to existing bolts locations on the tail end of the conveyor. The platform enables users to access the receiving hopper for

Telescoping Spout
A telescoping spout has been designed for applications that require specialized dust control. This unit can be attached to select models. The spout is connected to the PLC for automated control with an extension of up to 16ft. The spout can be retracted to a minimum of 4ft. Telescopic spouts are ideal for ship loading applications.

Belt Covers: Patented
Thor Global’s patented belt covers can be easily installed into any existing conveyor system. Ultra lightweight galvanized steel structural tubing and single bolt connections make these conveyor covers easy to handle, remove and assemble. Individual spring tensioning systems keep the covers secure and accessible for maintenance and repair. Lightweight UV resistant polyurethane material dramatically reduces wind load by 80%. Provides excellent dust control.

Mobile Truck Attachment
Thor has designed a unique attachment intended for shunt or goat truck vehicles. This simple attachment fits to a 5th wheel configuration, and enables the vehicle to lift and move the conveyor immediately. Thor’s mobile truck attachment is ideal for ship loading applications where shunt or goat truck vehicles are commonly used.
Spray Bar
Inner and outer telescopic truss configurations are available upon request.

Zero Speed Switches
Zero speed switches located on the inner and outer conveyor utilize PLC to detect if the belt is slipping and thereby prevent the stacker from overloading beyond its maximum capacity.